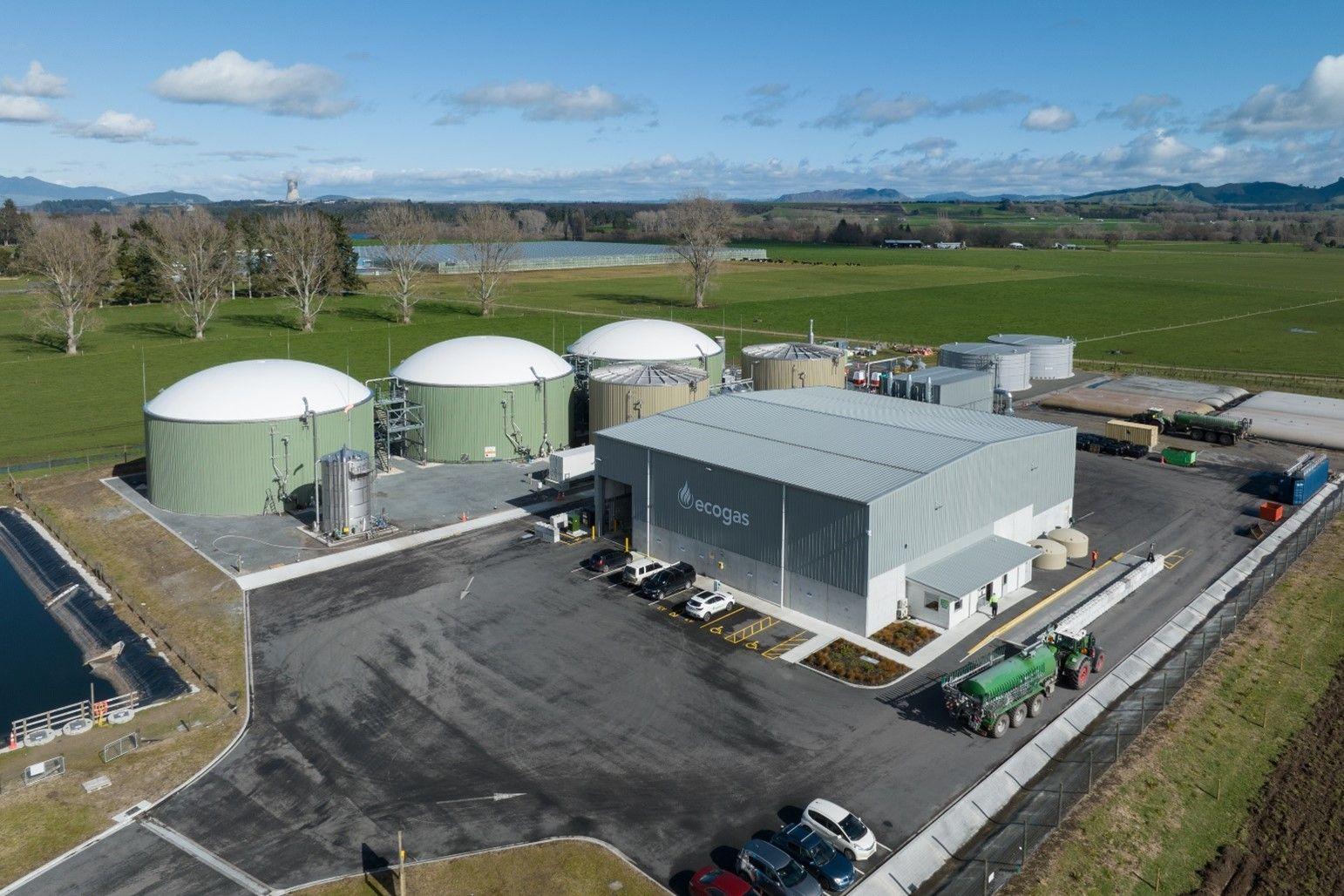
New Zealand’s first large-scale food waste-to-bioenergy facility
New Zealand’s first large-scale food waste-to-bioenergy facility, the Reporoa Organics Processing facility, has revolutionised food waste handling. The facility is designed to turn approximately 75,000 tonnes of organic waste from businesses and households across the North Island into sustainable renewable energy each year.
The facility is owned by Ecogas, a joint venture between Pioneer Energy and Ecostock Supplies, and situated on land owned by Turners & Growers (T&G), a New Zealand fresh produce business. T&G is leasing the land to Pioneer Energy and, in return, buying renewable electricity, heat and CO2 from Pioneer Energy to power its tomato glasshouses 450 metres from the facility.
From food waste to sustainable renewable energy
The facility uses acid phase and mesophilic anaerobic digestion to produce biogas, half of which is used in a combined heat and power (CHP) gas engine to generate renewable energy. The other half is upgraded to biomethane and injected into the adjacent natural gas pipeline. The energy generated from the CHP is used to operate the site and power up the equivalent of around 2,500 households in the region.
The CHP engine produces waste heat that is recovered as hot water at 90°C and circulated to the tomato hothouses during winter and cold nights to support growth.
The biomethane is blended at 30 barg into the natural gas pipeline serving local industry. The upgrading of the biomethane using high pressure membranes results in a waste stream of carbon dioxide which is cleaned at 940°C using a regenerative thermal oxidiser and then cooled and piped to the adjacent tomato glasshouses to also support growth. The digested sludge and separated digestate are used as a clean bio-fertiliser for approximately 2,000 hectares of local farmland.
AECOM brought together its process, mechanical, civil and electrical engineering specialists to design the biogas transfer pipelines, heat and CO2 transfer systems at the facility and the T&G glasshouses.
The finished system delivers 90°C water into the T&G thermocline buffer storage tank and cleaned pure CO2 to the T&G glasshouses during daylight to assist photosynthesis.
Cutting carbon and creating a circular economy
Using innovative technology and anaerobic digestion, the facility is expected to remove up to 10,000 tonnes of carbon dioxide annually and significantly reduce the amount of food waste that goes to landfill each year. The project highlights the benefits of a circular economy to reduce reliance on natural resources, reduce emissions and foster innovations towards a greener future.
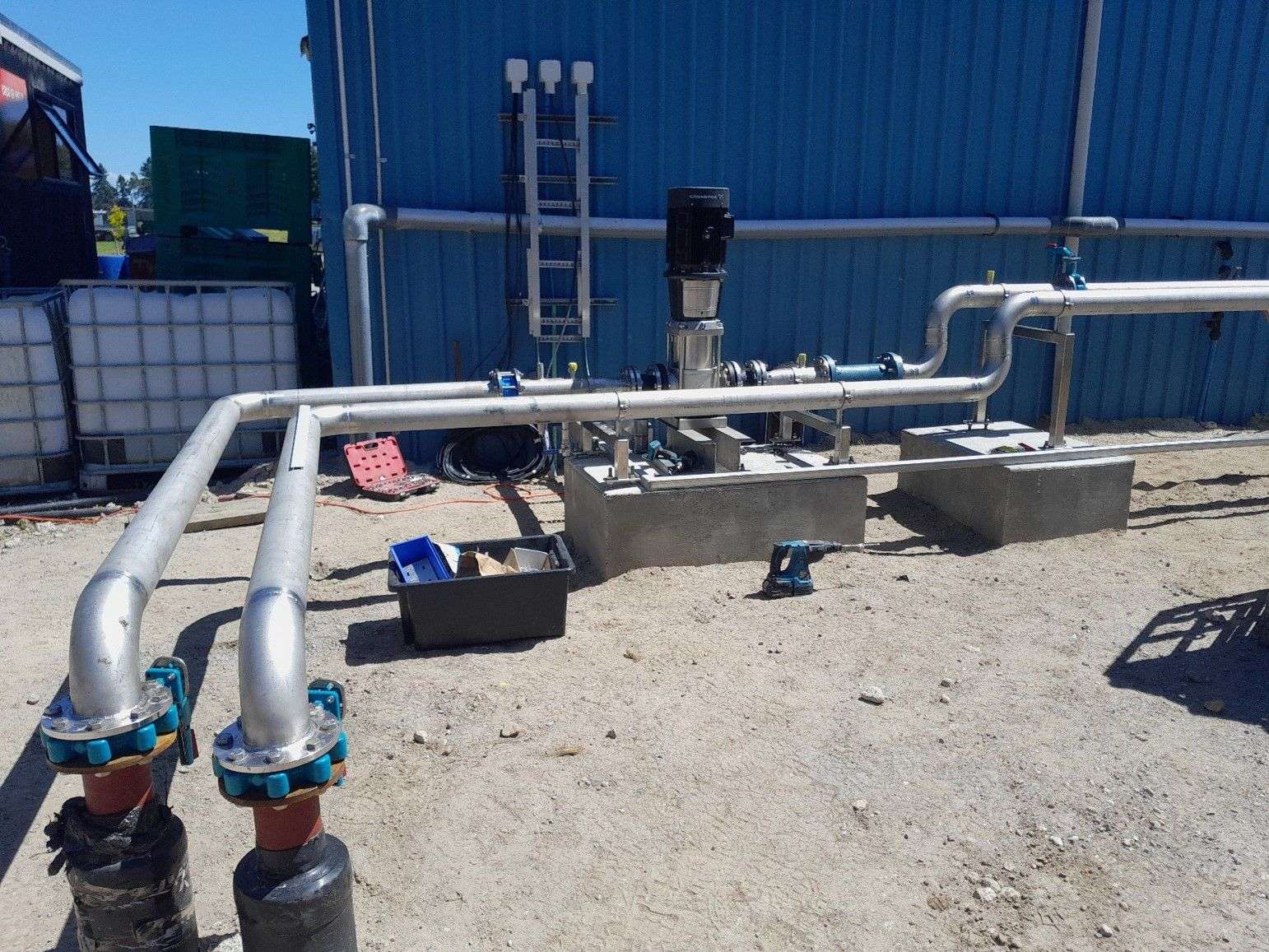